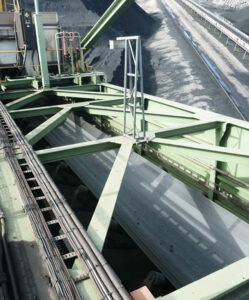
Bucket Wheel
iBelt installed right after the bucket wheel allows to measure volume flow and feed this back into the control loop for optimization of cutting depth and slew (reclaimers) as well as long travel (excavators) speed. Improvement potential is huge, customers report between 10% and 20% productivity increase and about 30% reduction of under- or overloading events on their belts.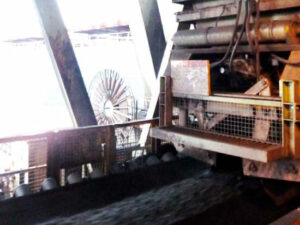
Reversing Conveyor
On reversing conveyors, iBelt measures the flow into the activated direction. Also iBelt detects when the conveyor runs and into which direction.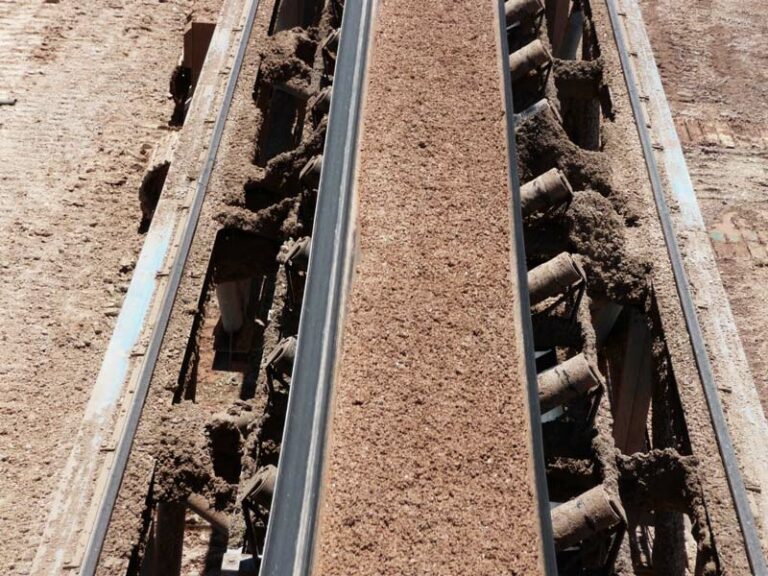
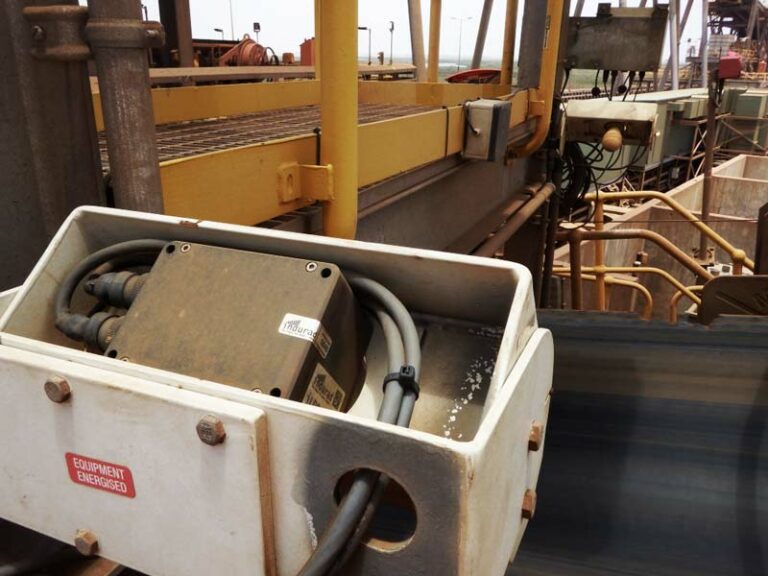
Misalignment Application
Misalignment of conveyor belts reduces lifetime and throughput, of the belt while increasing energy consumption. iBelt measures the belt position as well as the position of the material on the belt 4.000 times per second with a sub-millimeter (< 1 mm) precision. By having this real time information, chutes, transfer points, discharge belts or specialized idlers can be adjusted to make the belt fall back into its designated position in the girdlers.Stacker Travel Application
Volume flow measurement on the ingoing conveyor allows to regulate luff / long travel movements of stackers. Volume flow (m³/h) is provided to the stacker PLC to control the stacker.A-Frame Reclaimer
On an A-Frame reclaimer, the iBelt is mounted on the machine, thus measuring the exact volume flow from the reclaimer. This information is used to control the long travel and boom angle on the machine. Simple and efficient.Shiploader Application
While loading a ship, constant material flow is of utmost importance. The material flow into and out of surge bins can be monitored by indurad iBelts and thus controlled. iBelt helps to fill the belt – see above photograph – to its maximum capacity.Plant Flow Application
iBelt provides real time process data (volume, speed, …) about all belts within a plant (e.g. crushing area and foundry) to the SCADA system. Based on this information, automatic or manual decisions can be made in order to utilize the plant in the best way. An example is a Chilean copper mine in which the mills are the bottle neck of the entire mine. With our iBelt solution we can distribute optimum charge to the mills at any time.
Underground Logistics Application
iBelt also provides valuable process data for controlling underground conveyor belts. The indurad solution measures conveyed volume, speed, center of gravity, misalignment and freeboard and thus provides all parameters for an efficient conveyor belt control. The information is used in the conveyor belt PLCs, the SCADA systems as well as the in Manufacturing Execution System (MES). Thus several stakeholders profit from the system: operators, maintenance crews as well as (plant) managers.