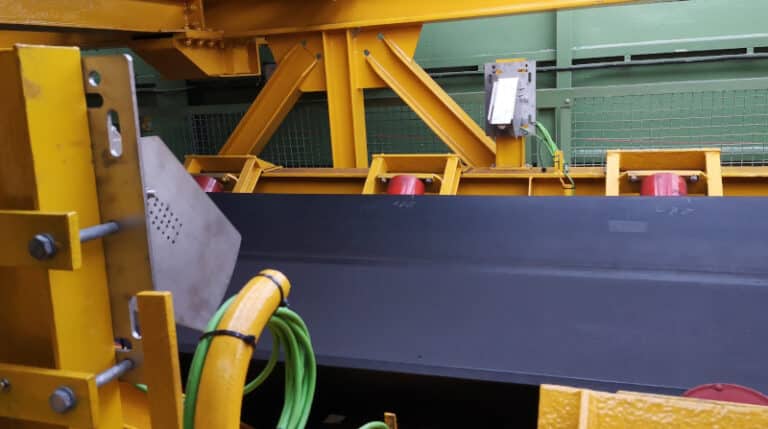
Guide-Plates
COUNTRY: Netherlands
MATERIAL: Coal
MACHINE: Barge loader
COMPONENTS: 2x iLDR-C
DESCRIPTION
iBelt measures belt alignment and material freeboard on boom belt, allowing for adapting machine control (guide plate positioning) to improve productivity, and to reduce wear.
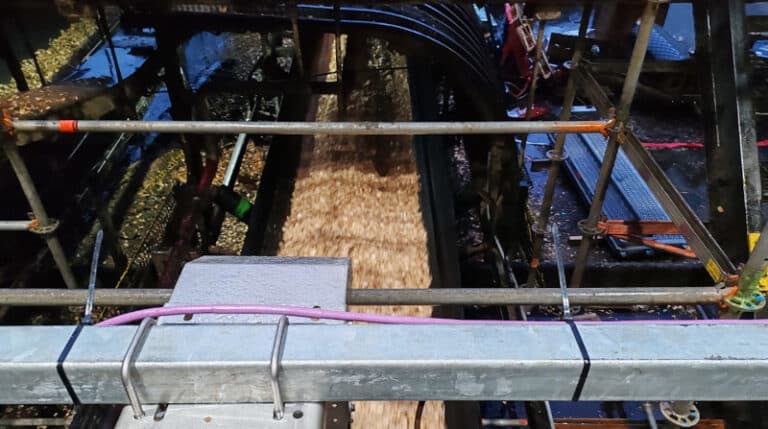
Wood Chips
COUNTRY: Chile
MATERIAL: Wood Chips
COMPONENTS: iSDR, iDVR, iRPU-F
DESCRIPTION
Volume-Flow measurement of wet wood chips.
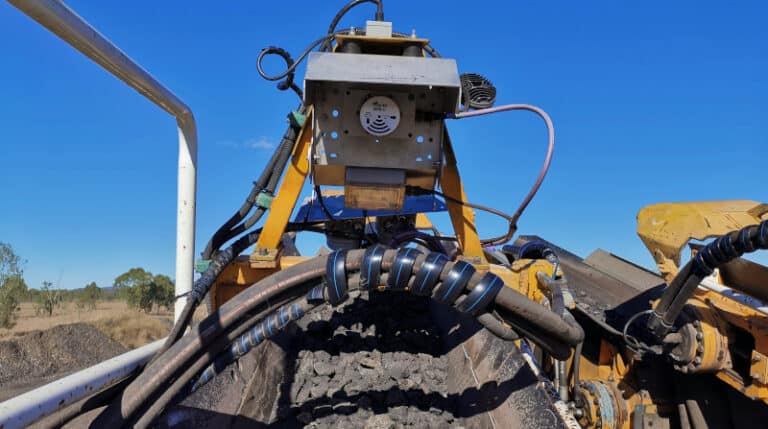
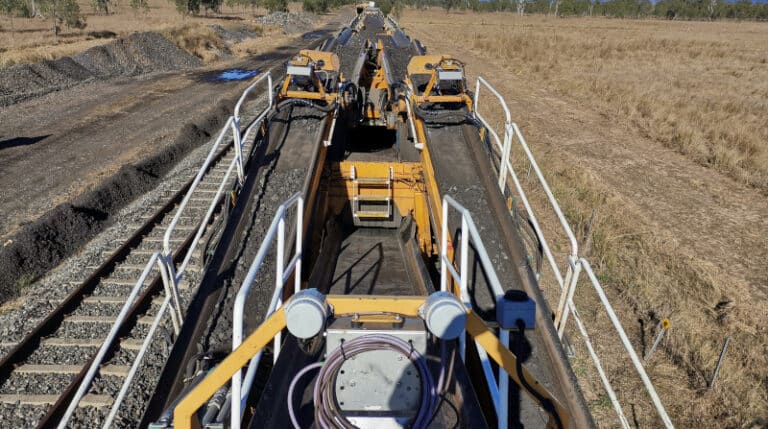
Train Tracks
COUNTRY: Australia
MATERIAL: Rocks
MACHINE: Track Renewal and Laying Machine
COMPONENTS: 3x iSDR-C and 3x iDVR
DESCRIPTION
iBelt measures and keeps track of reclaimed and distributed ballast material during track renewal.
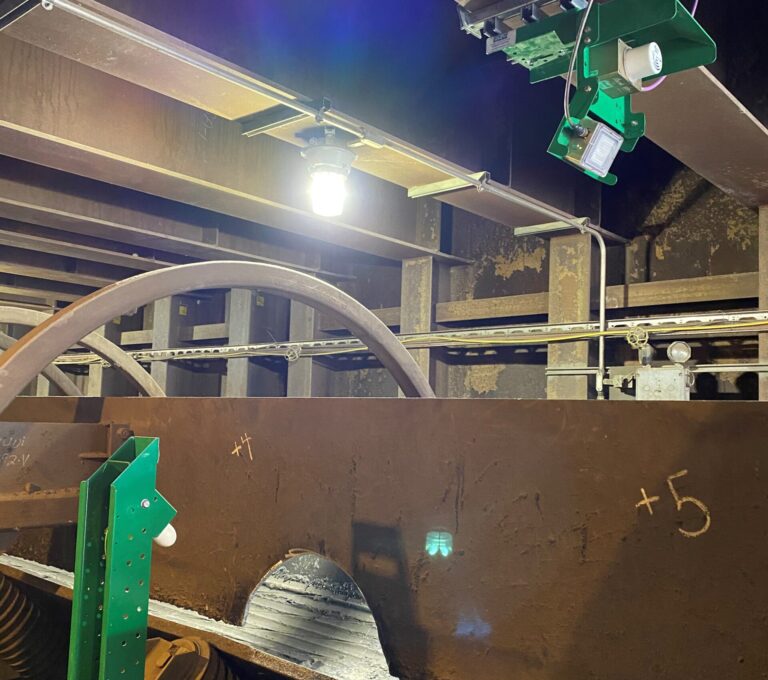
Oil Sand
COUNTRY: Canada
MATERIAL: Oil Sand / Tar Sand
COMPONENTS: 2x iLDR-C, iSDR-C, iDVR, iRPU-F
DESCRIPTION
Volumetric flow measurement and belt alignment tracking.
Extreme environmental conditions (dirt, temperature).
You are currently viewing a placeholder content from YouTube. To access the actual content, click the button below. Please note that doing so will share data with third-party providers.
More InformationCost down, revenue up
indurad is a leader in making mining and dry bulk handling or processing easier and more cost effective. Based on our radar technology we offer various solutions and also sensors with OEM interfaces such as ROS2.
Tar & Oil Sands
In Canadian oil sands operations iBelt measures the material throughput at several critical points: Flow from bin to crusher, alarms for overflow, blockage, empty. Flow into mixboxes, thus reducing massively the amount of steam needed. Filling of intermediate hoppers. On continuous miners: material disposed into trucks / performance of mining machines and contractors.Pulp & Paper
Measuring pulp and paper products with radar is a challenge. Due to indurad’s 77 GHz radar technology, our radar sensors are capable of measuring most wood products while e.g. dry cellulose is almost invisible to radar. Typical applications are: Canadian customers: To measure the volume flow of woodchips (inbound and outbound) for exact inventory information. European renewable power plant: Volumetric measurement data as a precondition for EU corporate sponsorship. Company delivers proof of compliance with EU legislation in the form of consumed material volume for eventual energy production.Potash & Fertilizers
Potash, salt and fertilizer mines and ports use iBelt for different purposes: Optimization of conveyor belt usage in mining operations, e.g. opening, closing of chutes, bunkers. Volumetric measurement for underground silos and domes – knowing how much material has been fed into the storage. Measuring volume loaded into barges and vessels. Productivity measurement of mining machines (roadheaders, rotorminers, K-Miners, …).Concrete & Cement
iBelt is the base for A-Frame reclaimer automation in cement plants as it measures the volume flow of reclaimed material directly on conveyor belt. Thus the PLC can control cutting depth of the reclaiming wheel and long travel speed of the machine and boom, increasing machine throughput (by about 20%) and reducing overloading of the conveyor as well as chute blockage.
Especially in cement plants, processes are better controlled by volume than tonnage, with the A-Frame reclaimers is being just one example of this.
Copper & Polymetallic
Chile’s largest copper mines use iBelt in several applications:
On tripper cars to control the speed of the tripper car for a homogeneous material discharging process into the stockpiles. Full automatization of tripper car – improved safety for workers.
Control of process chain after primary crushing: storage in silos/domes/stockpiles, feeding to mills, disposal to leach pads (stacker control).
On bucket wheel excavators for cutting depth automation and traversing travel optimization.
The volume, speed, misalignment data and freeboard measurements are provided in real time to the PLC, SCADA and MES systems for various purposes. Usually several departments benefit from the data (e.g. operations, maintenance, management). iBelt usually has a very short payback time, in most cases within months.
Especially in the copper industry, controlling processes by volume is better than controlling by tonnage as all process steps are based on volume (crusher feed, belt capacity, silos/domes/stockpiles, mills).